

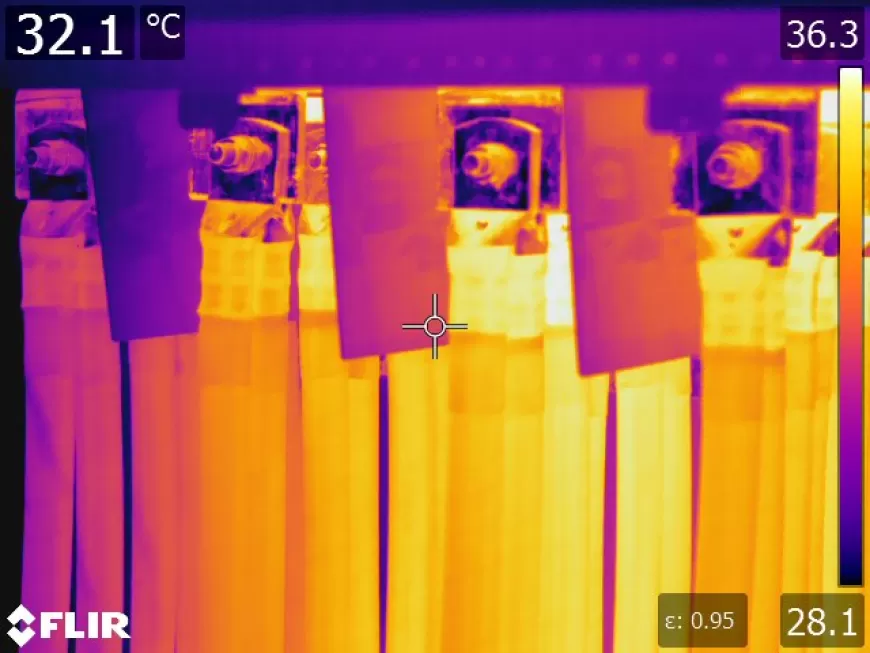


Infrared Thermal imaging analysis of electrical equipment and installations (Electrical Thermal Inspection) is probably the most common application of infrared thermography from many years. It is being used for inspection of both high voltage and low voltage installations. Transformers, over headlines, cabinets, switchgears, busbars, capacitor banks, MDBs, SMDBs, DBs and other electrical equipment’s can be tested using thermography cameras and can avoid catastrophic failures of equipment and fire incidents. Thermography is so useful on electrical equipment’s that it keeps the inspector at safe distance and it does not intrude upon electrical installations. Thermography should be done on live equipment with at least 60% load. Reports can be generated according to a classification criterion as per international standards or it can be generated as per customer’s classification criteria.
How Electrical Thermal Inspection is Done?
Electrical thermal inspection, also known as infrared thermography or thermal imaging, is a technique used to detect and identify potential issues in electrical systems by analyzing the temperature distribution of components and equipment. Here’s how the process is typically carried out:
Equipment Setup
Power-On
Scanning
Image Capture
Analysis
Interpretation
Reporting
It’s worth noting that electrical thermal inspections are often performed by trained professionals who have experience in interpreting thermal images and understanding electrical systems. Regular thermal inspections can help identify potential problems before they lead to equipment failures, malfunctions, or safety hazards.