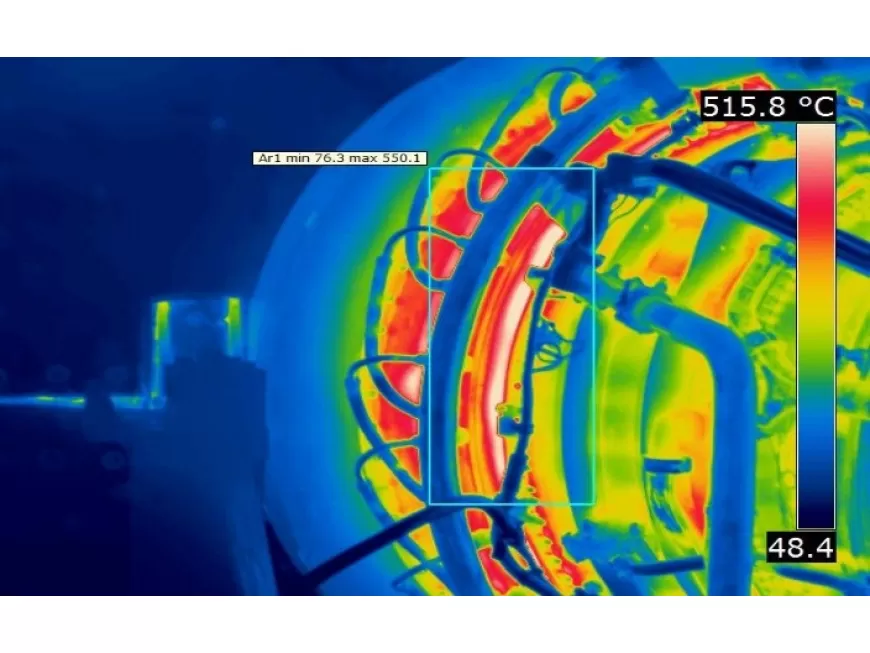
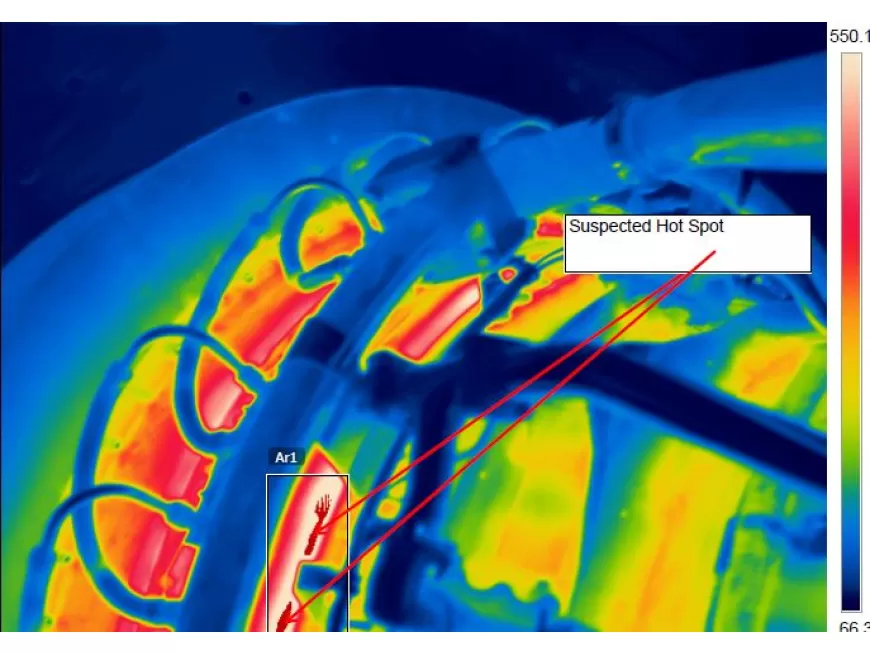
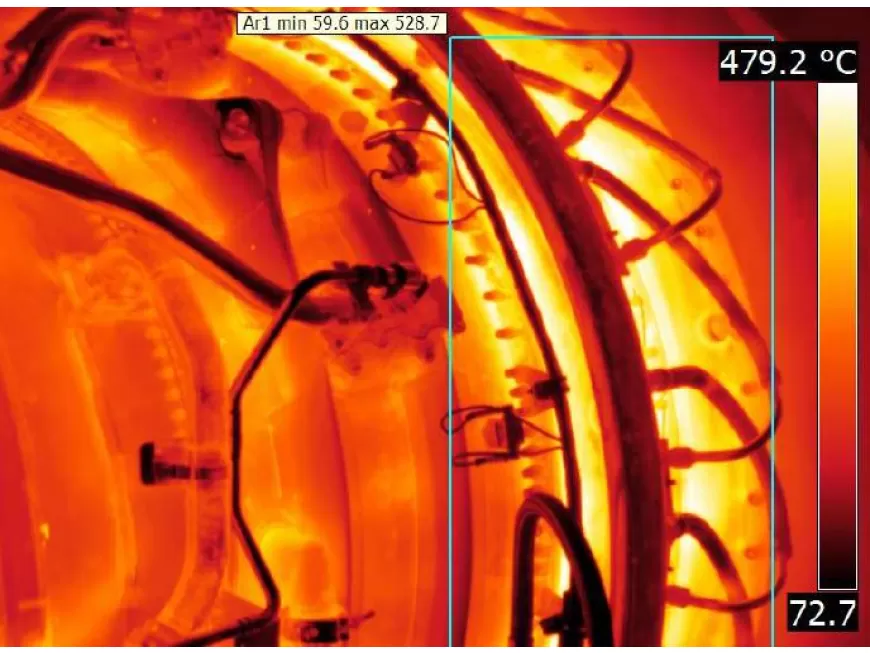

Thermal imaging is the only technology that allows operators to inspect all electrical and mechanical components of the turbine and the surrounding electrical system. Both for electrical and mechanical components, the general rule is that a component will become hot before it fails. Thermal imaging cameras spot this rise in temperature before a failure occurs. These hot spots will show up clearly in the thermal image.
A thermal camera can show gearbox and motor issues including shaft misalignments, as well as elusive electrical issues such as loose connections and imbalanced loads. The versatility of thermal cameras enables maintenance operators to make the most out of their preventive maintenance program.
Thermal Imaging camera also helps in detecting hotspots and insulation defects on the surface of steam and gas turbines thereby improving efficiency and performance of turbines.
Gas and steam turbine thermal inspections involve the use of thermal imaging technology to assess the performance, efficiency, and condition of gas and steam turbines. These inspections play a crucial role in detecting potential issues, optimizing turbine operation, and ensuring the reliability of power generation systems. Here are key points related to gas and steam turbine thermal inspections:
Purpose of Inspections
Thermal Imaging Technology
Components Inspected
Overheating Detection
Efficiency Optimization
Condition Monitoring
Non-Destructive Testing
Reporting and Documentation
Professional Inspection Services
Gas and steam turbine thermal inspections are essential for ensuring the efficient and reliable operation of power generation systems. By detecting overheating, identifying potential issues, and supporting maintenance strategies, these inspections contribute to optimized performance, reduced downtime, and increased turbine lifespan.